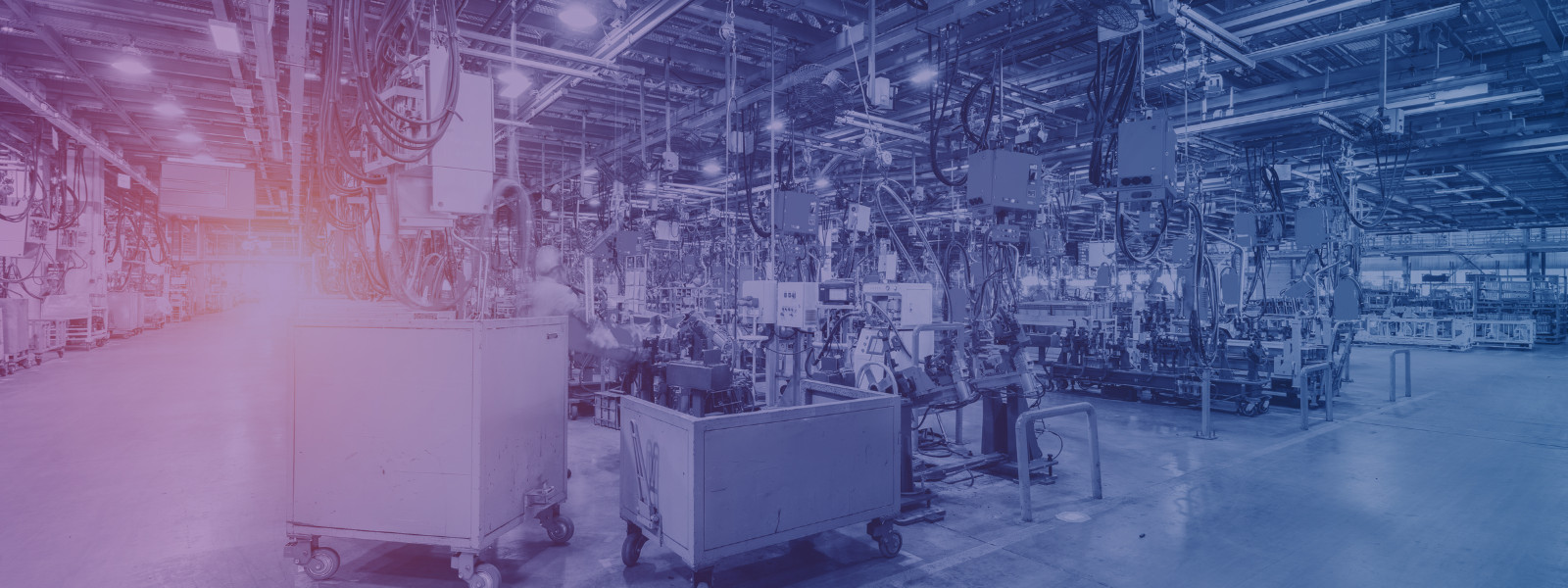
The UK manufacturing sector has perhaps never faced so many change dynamics - some positive but many negative. At a recent Made In Yorkshire round table event chaired by Steve Crow from Clarion, a discussion took place covering some of the issues impacting UK manufacturing and sharing best practice on ways to enhance business resilience in the face of change.
- Component supply - many manufacturing businesses use components either in their products or in manufacturing processes. Pre-Covid, Brexit and Suez Canal blockage the supply chain for electronic components may have been 6 - 12 weeks, but recent experience has seen this extend to over 60 weeks in some instances. This challenge in getting products to market, has required some organisations to rethink and redesign their products. Clarion are working in partnership with the likes of Arrow, one of the world’s largest suppliers of components, to support manufacturers to identify alternative solutions.
- Energy - it was recognised that energy is a particular issue for the whole sector, but accentuated in those organisations that are energy-intensive, such as polymer products and glass production. Energy costs are likely to continue to increase in the new year, and forward-thinking businesses are looking at strategies to reduce energy consumption to enhance their resilience, including the adoption of renewable technologies. ESG is an increasingly important issue for manufacturing businesses and this is often an important criteria in recruiting new talent into the business.
- Skills - there is still a massive skills shortage across most sectors, including manufacturing, and this has placed constraints on delivering business growth for many organisations. Manufacturers are having to think creatively about talent management and talent pipeline. This has included building stronger relationships with schools, colleges and universities, as well as looking into previously untapped resource pools. For example, some organisations are successfully recruiting ex-offenders and ex-military personnel. Increasingly, manufacturers are accelerating the adoption of robotics and automation to deal with the shortage of resource.
- Data - manufacturers are adopting new technologies to enhance business processes and efficiencies. This allows a better understanding of where incremental improvements can be made to enhance cost reduction or revenue enhancement.
- Rising material costs – the cost of materials and availability is an issue for many manufacturers. In many instances the costs can be passed on to customers but not in always, which will have a major impact on profit for businesses.
In summary; whilst there many ‘moving parts’ for manufacturers to deal with at the moment, many are investing in new innovations to mitigate risks or to find competitive advantage.
08/12/2022